高效革新:数字化工厂仿真软件赋能智能生产新纪元
19429202025-03-22安卓手游11 浏览
当传统制造业还在依赖人工经验和物理试错时,数字化工厂仿真软件已悄然掀起一场静默的革命。有人说它不过是“虚拟的游戏”,有人却认为它能颠覆制造业的未来。争议背后,一个事实不容忽视:全球智能工厂市场规模预计2025年将突破2000亿美元,而中国制造业数字化转型的渗透率仅为20%左右。这场革新究竟是“空中楼阁”,还是通向智能生产的必由之路?
1. 虚拟工厂能否替代真实产线?
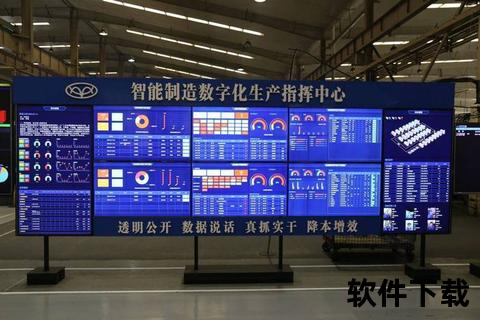
在传统认知中,工厂优化需要反复调试设备、消耗原材料,甚至停产改造。但数字化仿真技术打破了这一惯性。以上汽大众MEB智能工厂为例,其通过1400台工业机器人构建的“虚拟双胞胎”,在投产前已模拟了10万次生产场景。车身车间全球首创的在线绝对测量系统,通过实时数据校准将尺寸误差控制在0.1毫米以内,相当于人类头发丝的1/80。这种虚实结合的模式,让工厂调试周期缩短40%,能耗降低15%。
更令人惊叹的是西门子Plant Simulation的应用。某汽车零部件企业在软件中建立数字孪生模型后,发现某工位设备利用率仅为63%。通过模拟增加缓存区、调整物流路径,最终将利用率提升至89%,避免了一次耗资300万元的物理产线改造。这些案例证明,虚拟工厂不仅是真实世界的“预演场”,更是突破物理限制的“试验田”。
2. 数据驱动如何优化生产命脉?
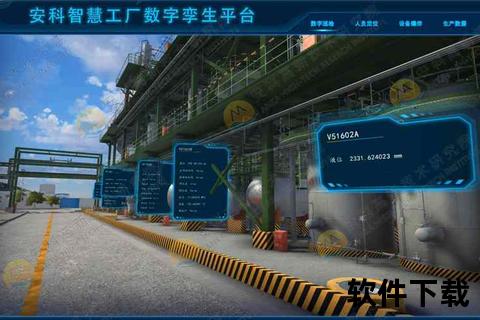
生产线的“黑箱”状态曾是制造业痛点。北京欧倍尔的智慧生产解决方案给出答案:通过自研通讯工具,将2000多个传感器数据实时映射到虚拟场景。某化工企业在软件中发现,反应釜温度曲线与理论值存在周期性偏差,最终追溯到冷却水阀门的0.5毫米机械磨损。这种微观洞察,让设备故障预测准确率从68%跃升至92%。
数据的价值不止于诊断。华为数字化工厂运用大数据分析,将生产计划排程从人工8小时缩减至系统自动生成的20分钟。更关键的是,系统能模拟供应链中断、设备故障等200余种突发状况,提前生成应对方案,使订单交付准时率提升至99.3%。这印证了高效革新:数字化工厂仿真软件赋能智能生产新纪元的核心逻辑——让数据成为决策的“第二大脑”。
3. 数字孪生如何打破行业壁垒?
从汽车制造到化工教育,数字孪生技术正在重构产业边界。路特斯全球智能工厂的3公里虚拟赛道,让车主在数字空间体验极限驾驶,同时收集的10万组数据反哺实车调校,使新品研发周期压缩30%。而在教育领域,安徽师范大学的煤制甲醇仿真工厂,用无毒物料模拟真实化学反应,学生失误率从35%降至5%,培养周期缩短50%。
更前瞻的实践出现在TCL空调武汉基地。其数字孪生系统将8条产线、16个实验室的数据流整合,实现从订单到交付的全流程可视化。当东南亚某国突发零部件短缺时,系统3分钟内完成全球供应链重组模拟,避免2000万元潜在损失。这种跨地域、跨层级的协同能力,标志着制造业进入“创新”时代。
通向未来的行动指南
高效革新:数字化工厂仿真软件赋能智能生产新纪元已成定局,但企业需警惕三大陷阱:一是盲目追求“全盘虚拟化”,忽视物理工厂的基础改造;二是数据孤岛导致“虚拟与现实脱节”;三是人才断层引发的“系统空转”。
建议采取“三步走”策略:
1. 选择性突破:优先在质检、物流等痛点环节部署仿真模块,如某企业通过AGV路径优化模块,3个月回收80%投资成本;
2. 数据筑基:建立标准化数据接口,确保虚拟模型与MES、ERP系统的双向联通;
3. 人才共生:借鉴岚图汽车的“数字工匠”计划,将一线操作员培养为“虚实双栖工程师”。
当数字孪生不再是实验室里的概念,当每个螺丝钉都在虚拟世界拥有“镜像”,这场静默的革新正悄然重塑制造业的DNA。或许正如李培根院士所言:“未来工厂的竞争力,将取决于它在数字空间中的进化速度。”