智能驱动CNC自动编程软件——革新性高效赋能未来智造
19429202025-03-26单机游戏10 浏览
传统CNC编程的瓶颈,智能驱动能否破局?
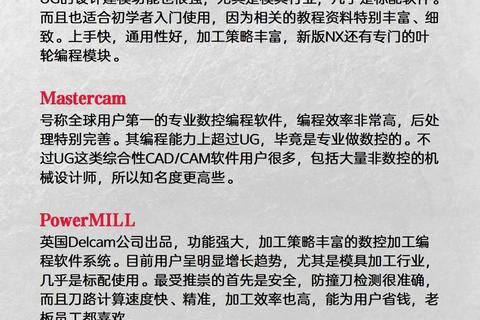
在制造业车间里,一位资深工程师可能需要花费数小时甚至数天时间编写一段复杂零件的加工程序。随着工业4.0浪潮席卷全球,一个问题浮出水面:当人工经验成为效率的枷锁,智能驱动的CNC自动编程软件能否成为制造业的“第二大脑”?
近年来,智能驱动CNC自动编程软件——革新性高效赋能未来智造的技术逐渐成熟。它不仅将编程时间缩短90%以上,更通过算法优化让加工精度突破人类极限。但质疑声始终存在:这些软件是否真能替代经验丰富的工程师?本文将通过实际案例与行业数据,解析这一技术如何重构制造逻辑。
1. 效率革命:算法如何超越人工经验?
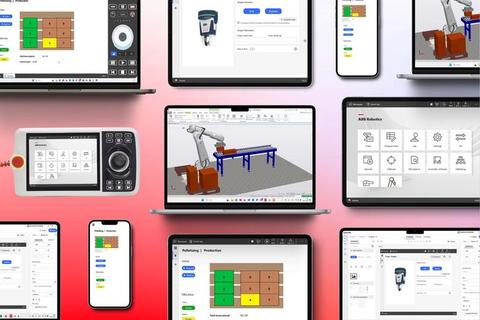
传统CNC编程依赖工程师手动计算刀具路径,而智能软件通过机器学习与大数据分析,可在数分钟内生成最优加工方案。例如某航空企业使用PowerMill软件加工涡轮叶片时,原本需要3天的五轴联动编程任务,被压缩至45分钟完成,刀具路径优化后材料损耗降低18%。
更惊人的案例来自西铁城精机的Cincom自动车床。该设备搭载的智能编程系统通过机内测量技术,每加工250个零件自动触发一次精度校准,将连续不良品数量从500个降至0,直接减少75%的检测工时。这些数据印证了智能驱动CNC自动编程软件——革新性高效赋能未来智造的核心价值:用确定性算法替代人工试错。
2. 复杂工艺:智能系统怎样突破技术极限?
面对航天发动机喷管这类含数百个曲面的超复杂零件,人类工程师往往束手无策。Autodesk Fusion 360的解决方案是:通过云端算力实时解析3D模型特征,自动生成分层切削策略。某卫星制造商应用该技术后,成功将直径2米的钛合金构件加工误差控制在±0.005mm,相当于头发丝的1/15。
在汽车模具领域,Mastercam的动态铣削功能展现了另一维度突破。其智能算法可根据材料硬度动态调整进给率,在加工高碳钢时,主轴负载波动从30%降至5%,刀具寿命延长3倍。这些案例揭示了一个趋势:智能驱动CNC自动编程软件——革新性高效赋能未来智造,正在将“不可能加工”变为“标准化操作”。
3. 生态重构:智能工厂需要怎样的新基建?
广东某智能工厂的实践极具代表性。他们采用复合机器人AMR+PowerMill的组合方案,实现24小时无人化生产。视觉识别系统与加工参数的实时联动,使换型时间从2小时缩短至15分钟,设备综合效率(OEE)提升至89%。这套系统背后的支撑,正是智能编程软件与物联网设备的深度整合。
2025年机床加工参数智能软件行业报告显示,采用云端协同技术的企业,新产品试制周期平均缩短40%。例如某数控车床软件通过接入工业互联网平台,可调用2000多种材料数据库,自动匹配切削参数,使新手操作员也能达到高级技师的加工水准。这标志着制造业正在形成“软件定义制造”的新范式。
智造未来:企业如何搭上转型快车?
对于准备拥抱智能驱动的企业,建议分三步走:
1. 选型匹配:中小型企业可优先考虑Fusion 360等集成化平台(学习周期<3天),大型企业宜选择PowerMill+AMR机器人等定制方案
2. 人才储备:建立“工艺工程师+软件工程师”的复合团队,重点培养G代码优化与算法调参能力
3. 技术迭代:每季度更新加工参数库,接入机床健康监测系统实现预测性维护
当东莞某五金厂通过智能编程软件将月产能从5万件提升至12万件时,厂长感慨:“这不是机器替代人,而是给人装上了翅膀。”智能驱动CNC自动编程软件——革新性高效赋能未来智造,正在重塑的不仅是生产效率,更是整个制造业的价值链逻辑。在这场变革中,早一步行动的企业,或将定义下一个十年的行业规则。