智能革新驱动未来:高效精准齿轮设计软件领航工业制造新纪元
19429202025-03-21手机软件20 浏览
一、传统齿轮设计为何难以突破效率瓶颈?
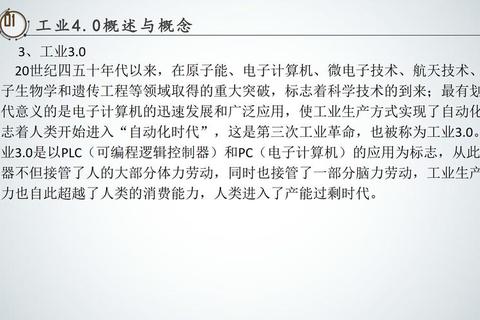
当全球制造业以每年5%的增速扩张时,一个令人费解的现象却在持续:超过60%的齿轮制造企业仍在使用二十年前的设计方法。手工计算、二维图纸、反复试制的传统模式,不仅导致新产品研发周期长达3-6个月,更让中国齿轮行业每年因设计误差造成的材料浪费高达12亿元。这种低效困局背后,是否意味着工业基础件的设计革命已经迫在眉睫?
智能革新驱动未来:高效精准齿轮设计软件领航工业制造新纪元的实践给出了明确答案。郑州机械研究所研发的ZGCAD系统,通过集成有限元分析和参数化建模技术,将行星齿轮箱的设计周期从45天压缩至7天。该系统在国内600余家齿轮厂的推广应用证明,采用智能设计软件的企业平均生产效率提升73%,材料利用率提高28%。在浙江某变速箱制造企业,设计人员通过软件内置的遗传算法,仅用3次迭代就优化出承载能力提升19%的斜齿轮参数组合,而传统方法需要反复试制15组样品。
二、微米级精度如何从理想变为现实?
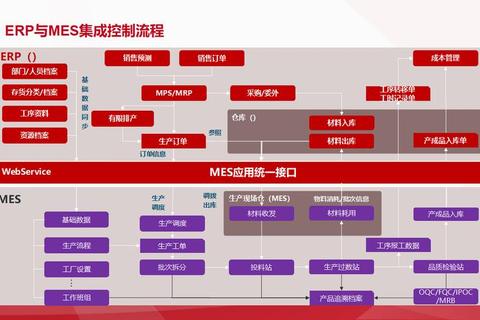
在新能源汽车减速器齿轮的制造领域,0.005mm的齿形误差就可能导致传动系统异响。日本电产新宝公司曾对中国供应商提出齿面粗糙度Ra0.4μm的严苛要求,这相当于头发丝直径的1/200。平湖一鑫齿轮借助埃马克K160数控滚齿机的智能化补偿系统,不仅将加工精度稳定控制在±2μm,更通过云端数据追溯实现了百万级产量零缺陷交付。德国克林根贝格的KIMoS软件,通过数字孪生技术模拟出齿轮副的接触应力分布,使行星齿轮的啮合噪音降低12dB,相当于将车间环境从闹市街头变为图书馆。
这种精度革命正在重构产业格局。2024年国内齿轮行业数据显示,采用智能设计软件的企业,其产品首次装机合格率从78%跃升至96%,售后服务成本下降41%。更值得关注的是,某军工企业利用拓扑优化算法设计的航天齿轮,在保持同等强度的前提下成功减重37%,这相当于让卫星有效载荷增加了一个高清遥感相机。
三、智能工厂的齿轮如何自主进化?
在重庆某智能装备产业园,一组令人震撼的数据正在改写制造逻辑:50台数控机床通过工业物联网连接,实时采集的2000多个传感器数据,经云端AI分析后自动优化切削参数。这使得滚齿刀寿命从3000件提升到8500件,每年节省刀具成本260万元。更前沿的探索发生在3D打印齿轮领域,西安增材制造国家研究院通过机器学习算法,让渐变模数齿轮的晶格结构实现应力自适应分布,创造出传统工艺无法实现的超静音传动系统。
数字孪生技术的深度应用,使得齿轮设计从静态图纸转变为动态生命体。上海电气开发的齿轮箱健康管理系统,能提前2000小时预警潜在故障,将风力发电机的维护成本降低45%。这种"会思考的齿轮"正在催生新的商业模式,某德国企业已开始按传动系统运行小时数收费,而不是简单售卖齿轮产品。
智能革新驱动未来:高效精准齿轮设计软件领航工业制造新纪元的实践揭示,制造业的智能化转型绝非简单的机器换人。建议企业分三步构建竞争力:首先部署模块化设计平台降低入门门槛;其次建立数据中台沉淀工艺经验;最终通过数字孪生实现产品全生命周期管理。正如汽车齿轮龙头企业双环传动的转型经验所示,当设计效率提升与智能制造系统形成闭环,传统制造企业也能在工业4.0浪潮中占据先机。这场始于齿轮设计软件的变革,终将重塑整个工业制造的DNA。