高效能智能驱动加工中心编程软件极速优化新标杆
19429202025-03-23苹果软件18 浏览
一、传统编程效率低下,制造业还能跟上智能时代吗?
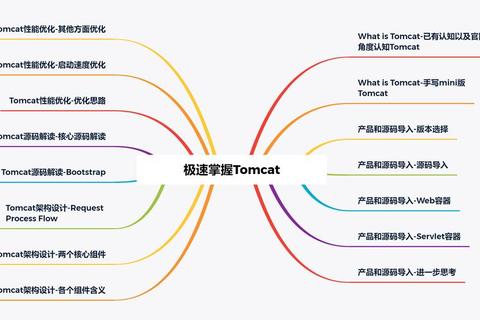
在制造业数字化转型的浪潮中,一个争议性问题浮出水面:面对日益复杂的加工需求,传统编程软件依赖人工经验、耗时耗力的模式,是否已成为制约生产效率的瓶颈?某汽车零部件企业曾公开数据:一套普通模具的编程耗时长达40小时,且因参数误差导致的返工率高达15%。而随着“高效能智能驱动加工中心编程软件极速优化新标杆”的出现,这一局面正在被颠覆。
二、智能算法如何让加工路径缩短30%?
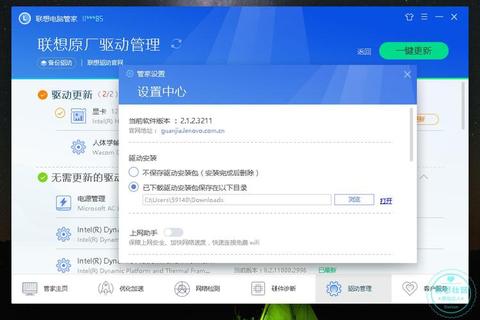
传统编程中,加工路径规划依赖工程师经验,而智能算法通过实时分析材料特性、刀具磨损数据及机床负载,能自动生成最优路径。以Cimatron E9为例,其新增的随形清根策略和五轴毛坯识别功能,使某航空航天企业的叶轮加工时间从8小时降至5.5小时,效率提升31%。更值得关注的是,这类软件通过机器学习积累历史数据,例如WorkNC在某德国汽车模具厂的案例显示,连续加工100组相似零件后,系统可自动预测刀具寿命并调整进给速率,将整体加工周期压缩28%。
三、自动化工具如何实现“零干预”编程?
“高效能智能驱动加工中心编程软件极速优化新标杆”的核心突破在于将人工操作转化为自动化流程。某医疗设备厂商使用Cimatron的电极设计模块时,通过镜像拷贝和快速模板功能,将原本需要2天的电极编程缩短至3小时,且系统自动生成CMM检测路径,确保精度误差小于0.005mm。而在模具行业,WorkNC的动态库存模型管理功能,允许实时更新毛坯数据,重庆某压铸企业借此实现24小时连续加工,人力成本降低40%。这些案例印证了AI驱动的自动化不仅是工具升级,更是生产模式的革命。
四、数据孤岛打破后,跨平台协作有何新可能?
传统CAM软件与CAD、CAE系统数据割裂,导致重复建模和兼容性问题。新一代软件如Mastercam 2025,通过PMI(产品制造信息)功能直接读取Catia、UG的设计参数,使某新能源电池壳体企业的模型转换时间从6小时降至20分钟。更前沿的应用体现在云端协同——某机床厂商利用AI驱动的数据接口,将分布在3个国家的设计、编程、加工团队整合至同一平台,项目交付周期缩短50%。这种全链路数据贯通,标志着制造业正式进入“协作”时代。
未来之路:企业如何抓住智能编程红利?
对于制造企业而言,拥抱“高效能智能驱动加工中心编程软件极速优化新标杆”需采取三步策略:
1. 功能优先验证:选择支持五轴联动、AI参数优化、跨平台数据接口的软件,参考华为云CodeArts IDE的“实战对比测试法”,用企业典型零件进行48小时深度试用;
2. 人才梯队重构:建立“AI辅助+人工复核”机制,如重庆横河川仪公司通过内部培训,使工程师在3个月内掌握智能编程工具,错误率降低至0.3%;
3. 生态协同布局:优先接入工业互联网平台,例如忽米网的“5G+AI”解决方案,可实现设备状态监控与编程参数动态调整的闭环管理。
在这场智能制造的竞赛中,唯有将技术革新与生产实践深度融合的企业,才能在新一轮工业革命中占据制高点。而“高效能智能驱动加工中心编程软件极速优化新标杆”,正成为这场变革中最关键的加速器。