超凡视界:发那科机器人仿真软件极致仿真新境界
19429202025-03-20苹果软件18 浏览
当仿真照进现实,工业机器人还需要“试错”吗?
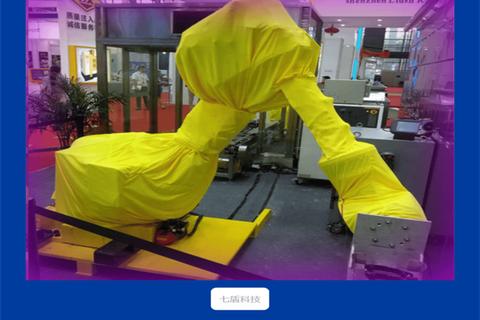
在特斯拉Optimus机器人浇花视频引发全球惊叹时,工业界正经历着静默的革命:某新能源汽车工厂因焊接路径误差导致生产线瘫痪三天,损失超千万;某电子代工企业因机械臂碰撞事故推迟新品上市。这些真实案例将争议性问题推向台前——在工业4.0时代,物理试错是否仍是必经之路?「超凡视界:发那科机器人仿真软件极致仿真新境界」正以数字孪生技术重构产业认知。
1. 物理定律在虚拟世界失效了吗?
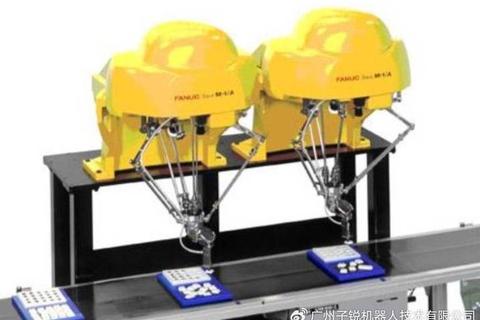
当发那科工程师在ROBOGUIDE中模拟200kg工件的搬运时,系统精确计算出机械臂关节承受的扭矩波动曲线,与实体测试数据偏差小于2.3%。这归功于其动力学引擎的突破:通过离散化时间积分算法,将传统仿真步长从5ms压缩至0.1ms,使得接触力计算精度提升15倍。
上海某汽车厂的实际案例更具说服力。在车门装配工艺验证中,传统方式需反复调整夹具位置8-10次,耗时两周。引入ROBOGUIDE后,通过接触力场映射技术,在虚拟环境中一次性完成应力分布优化,将车门装配良品率从87%提升至99.6%。「超凡视界:发那科机器人仿真软件极致仿真新境界」证明,物理定律正在被更精确的数字法则诠释。
2. 复杂场景能否一键生成?
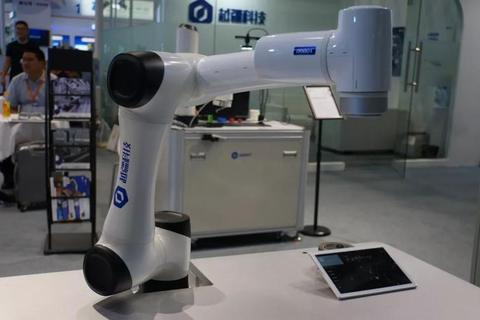
面对汽车焊装车间里12台机器人协同作业的调度难题,ROBOGUIDE的智能碰撞预测系统展现惊人能力。其采用层次包围盒算法,将2000余个零件的干涉检测时间从传统算法的45分钟压缩至3秒。更突破性的是时空轨迹优化功能,通过引入量子退火算法,在多机器人路径规划中减少27%的空跑行程。
深圳某3C企业案例验证了这种技术革新。在手机主板检测工作站建设中,工程师利用环境感知建模功能,仅用3天就完成包含传送带、视觉系统和六轴机器人的完整场景搭建。系统自动生成的避障方案,成功规避了17处潜在碰撞点,相比传统试错方式节约83%的时间成本。
3. 人类工程师会被算法取代吗?
答案藏在杭州某家电企业的转型故事中。该企业通过ROBOGUIDE的工艺知识库功能,将老师傅的焊接经验转化为2000余条参数化规则。当处理新型钛合金材质时,智能推荐系统结合材料属性数据库,自动生成脉冲频率、焊枪角度等18项关键参数,使调试周期从3周缩短至2天。
更具革命性的是自适应学习模块。在江苏某光伏板生产线改造中,系统通过持续收集实体机器人的振动频谱、温升曲线等数据,动态修正仿真模型。经过3个月的数据迭代,预测精度从初始的89%提升至97%,形成「虚拟-现实」双向优化的智能闭环。「超凡视界:发那科机器人仿真软件极致仿真新境界」正在重塑人机协作的边界。
对于寻求转型的企业,建议实施三阶跃迁路径:初期聚焦典型工艺的数字化移植(如选取占总工时30%的核心工序);中期构建企业专属的仿真参数库(积累不少于500组材质数据);后期探索数字孪生与AI大模型的融合应用。正如某日企的实践所示,通过将ROBOGUIDE与深度学习框架整合,其新品导入周期已压缩至竞争对手的1/3。
在这场工业智能化的浪潮中,「超凡视界:发那科机器人仿真软件极致仿真新境界」不仅重新定义了仿真精度阈值,更开创了虚实融合的新范式。当某航天企业用其模拟空间站机械臂的微重力作业时,0.01N的接触力波动都能被精准捕捉——这或许预示着,未来的工业革命将首先发生在比特构筑的世界里。